These challenges create a clear need for innovation in warehouse safety technology, particularly solutions that can provide comprehensive, continuous monitoring while enabling proactive accident prevention.
Average cost per workplace injury:
$40,000
Annual increase in insurance premiums:
10-15%
Workplace injury rate in warehouses:
6.1 per 100 workers
Lost productivity due to safety incidents:
20-30 days per case
Compliance violation penalties:
up to $1.5 million
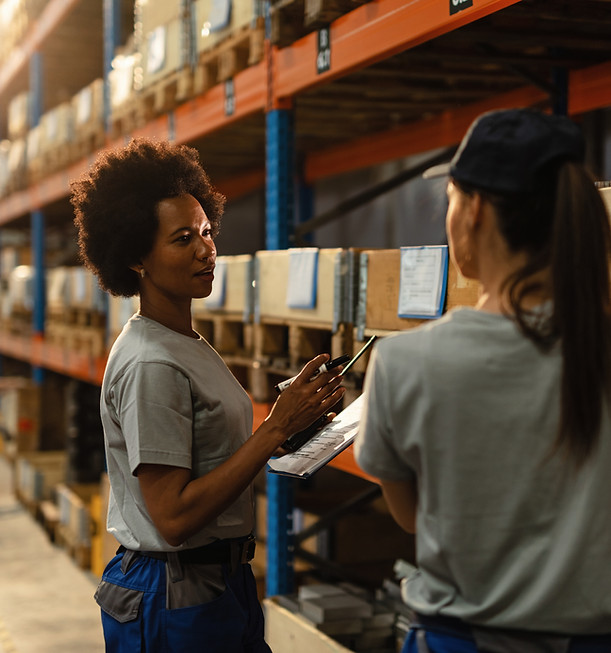
The Challenge
Current Challenges
Relying on human observation can result in lapses, especially in high-demand environments where constant vigilance is challenging. This inconsistency leaves room for safety risks to go unnoticed.
Without real-time hazard detection, response times can lag, increasing the likelihood of accidents and injuries when risks are not immediately identified and addressed.
During shift transitions or breaks, safety monitoring often pauses, creating vulnerable periods when potential hazards may arise unnoticed.
In expansive facilities, implementing and maintaining uniform safety standards is a logistical challenge, with different areas potentially having varied levels of oversight.
Reactive systems focus on responding to incidents rather than preventing them, limiting the ability to foresee risks and intervene before accidents occur.
Keeping up with evolving safety regulations demands extensive resources and increases the complexity of compliance, making it challenging to stay current without straining resources.
As risks increase, so do insurance premiums and liability costs, adding financial pressure to maintain adequate safety practices and minimize liability.
Supervisors tasked with enforcing safety protocols are often stretched thin, managing multiple responsibilities alongside maintaining a safe environment.

Why Warehouse Safety Needs Innovation
The warehouse industry stands at a critical juncture where traditional safety measures no longer suffice in addressing modern operational challenges. The scale and complexity of contemporary warehouse operations, combined with increasing pressure for efficiency and speed, have created an environment where conventional safety approaches are proving inadequate and increasingly costly.
Recent industry statistics paint a concerning picture of the current state of warehouse safety. In Canada alone, over 10,000 warehouse-related injuries were reported in 2022, resulting in an estimated $5 billion in annual costs to businesses. The situation in the United States is even more dramatic, with businesses facing over $50 billion in annual costs associated with safety non-compliance, injuries, and penalties. Perhaps most striking is the fact that 94% of workplace accidents are preventable with proper protocols and timely intervention.
The rapid evolution of warehouse operations has introduced new challenges that traditional safety measures struggle to address. As facilities grow larger and more complex, manual monitoring becomes increasingly ineffective. The introduction of automated systems and the pressure to maintain high-speed operations create new safety risks that require more sophisticated monitoring and prevention strategies.

The Challenge
The Financial Impact
Workplace injuries lead to immediate costs, including medical expenses, compensation, and operational disruptions, all of which directly impact the bottom line.
Injury rates and safety records significantly influence insurance premiums, with frequent incidents driving costs up and impacting the organization’s profitability.
Non-compliance with safety standards can lead to substantial fines and legal fees, making adherence to regulations essential to avoid financial penalties.
Accidents disrupt workflows, leading to lost productivity and downtime that can affect operational efficiency and reduce output.
Compensation claims following incidents are costly, with additional expenses for recovery, rehabilitation, and potentially hiring replacements.
Injuries often necessitate retraining or hiring replacements, leading to further costs for onboarding and training to fill gaps left by absent workers.
Managing safety documentation, incident reports, and compliance records adds to the administrative load, diverting resources from other critical functions.
Safety incidents can tarnish an organization’s reputation, affecting relationships with clients and partners and potentially leading to lost business.

The Challenge
Operational Limitations
Human-based monitoring is limited by working hours, making it impossible to ensure continuous safety oversight without automated solutions.
While CCTV cameras capture footage, they are reactive, providing evidence only after incidents occur rather than preventing them in real-time.
Safety audits, though valuable, occur at intervals, leaving gaps in between that may allow new risks to go unaddressed.
While essential, training cannot cover every scenario, and over time, workers may become less vigilant without continuous reinforcement.
Documenting incidents and safety protocols on paper is time-consuming, harder to analyze, and increases the risk of data loss.
Without digital tracking, it’s challenging to analyze trends or predict future risks, limiting the ability to prevent recurring incidents.
Traditional systems address incidents only after they occur, lacking the proactive capabilities needed to anticipate and prevent accidents.
Standardizing safety measures across diverse teams and areas is complex, often resulting in inconsistent application and enforcement.